PIC houses Malaysia's only integrated refinery, steam cracker and petrochemical plants, with the capacity to provide a reliable supply of feedstock.
The Refinery Complex and selected petrochemical plants are owned and operated by Pengerang Refining Company Sdn Bhd and Pengerang Petrochemical Sdn Bhd (collectively known as PRefChem), a joint venture between PETRONAS and Saudi Aramco.
At the heart of PIC is the Refinery Complex, the fourth largest in Southeast Asia.
This full conversion complex processes up to 300,000 barrels per day (bpd) of various crudes.
Critical units in the refinery have a multiple train configuration to ensure that production is uninterrupted to offer the highest levels of reliability.
The Steam Cracker Complex is the single largest plant in PIC, providing feedstock to the Petrochemical Complex. Products include olefins, ethylene, propylene, butadiene and pyrolysis gasoline.
The Petrochemical Complex in PIC comprises three main facilities - polymers, glycols and C4 derivatives.
Together, they produce over three million tonnes of a variety of petrochemicals - polypropylene, polyethylene, ethylene glycols and C4 isononanol - all important ingredients for millions of end-consumer products essential to today's modern living.
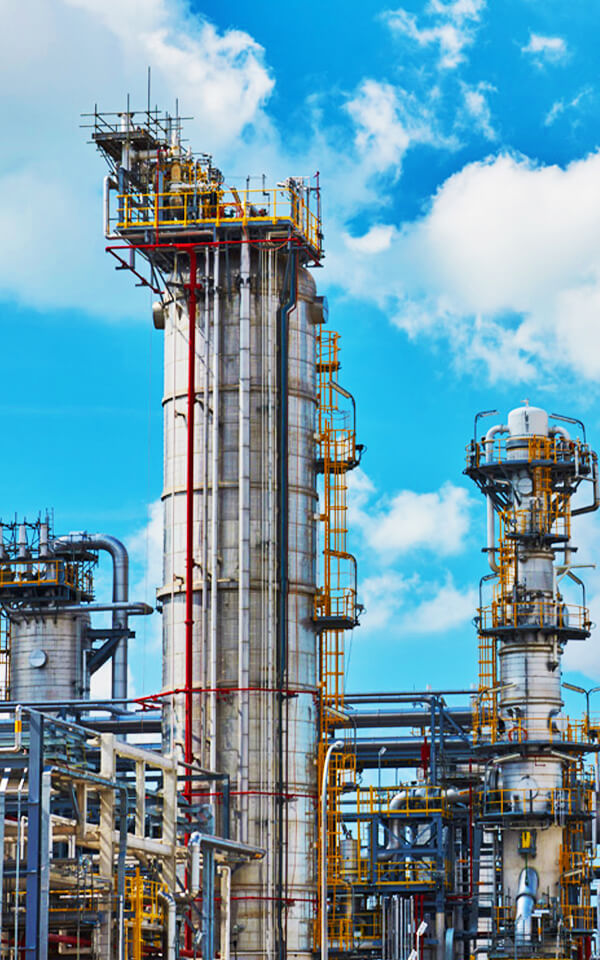
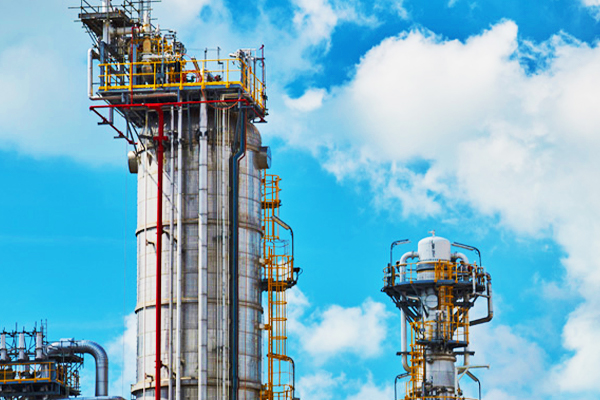
The Refinery Complex features world class technology licensors such as Axens, Chevron, Haldor Topsoe, Technip-Benelux, UOP and Linde. These provide a high degree of reliability, backed by excellent technical services.
The complex has multiple trains to ensure enhanced production reliability. Some of its process units are unique to the refinery, with technologies applied for the first time in Malaysia.
For example, its two-train residual fluid catalytic cracker (RFCC) unit uses Axens technology, a first in Malaysian oil refining. Its 140,000 bpd capacity makes the RFCC the single largest facility that uses this particular technology.
Another unique feature of the refinery is the Kerosene HydroTreater (KHT), uniquely designed to produce dual purpose kerosene for jet fuels, as well as for domestic uses.
The refinery’s naphtha hydro-treating unit is also the first of its kind in the country that uses Axens technology. The unit purifies naphtha with a feed capacity of 21,000 bpd to generate more gasoline.
Another novel technology is the resin-based amine reclaiming facility, which continuously cleans the amine solvent and prevents the traditional problem of foaming in the absorbers.
PETRONAS’ in-house technologies are also widely employed. For instance, advanced high-efficiency trays have been installed in the distillations columns to maximise process efficiency.
Emissions from the refinery comply with stringent international standards, and Zero Flaring is made possible by a Flare Gas Recovery System (FGRS).
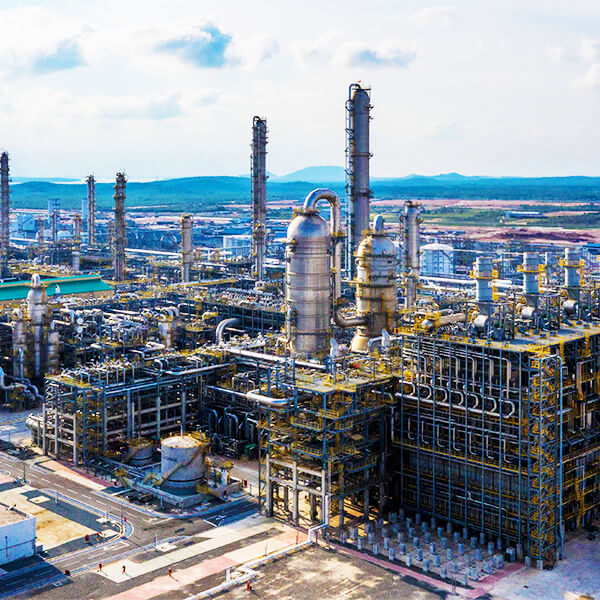
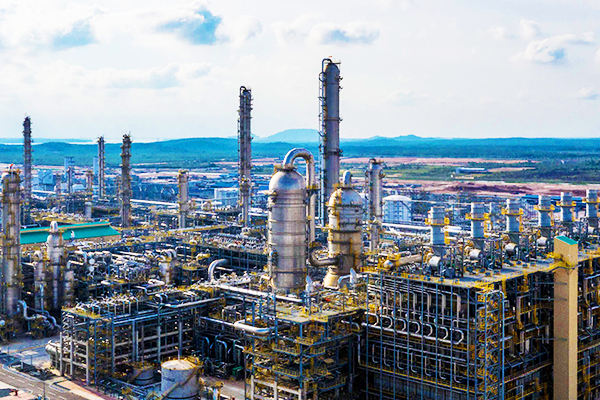
The Steam Cracker Complex uses state-of-the-art Lummus technology.
As steam cracking is the single most energy-consuming process in the chemical industry, advanced naphtha cracking technologies are therefore needed to drastically reduce energy consumption. For example, in the pyrolysis section, usage of advanced coil and furnace materials translates into major energy savings.
The furnaces at the complex, the largest installed in Malaysia, are designed to have a maximum efficiency of 94.5%. They feature low nitrogen burners to minimise emissions. Its major compressors, charge gas compressor and binary refrigeration are also more than 85% efficient.
The refrigeration system in the Steam Cracker Unit combines the conventional cascaded refrigeration systems into a single system with three components - methane, ethylene and propylene - thereby reducing the number of compressors and the footprint.
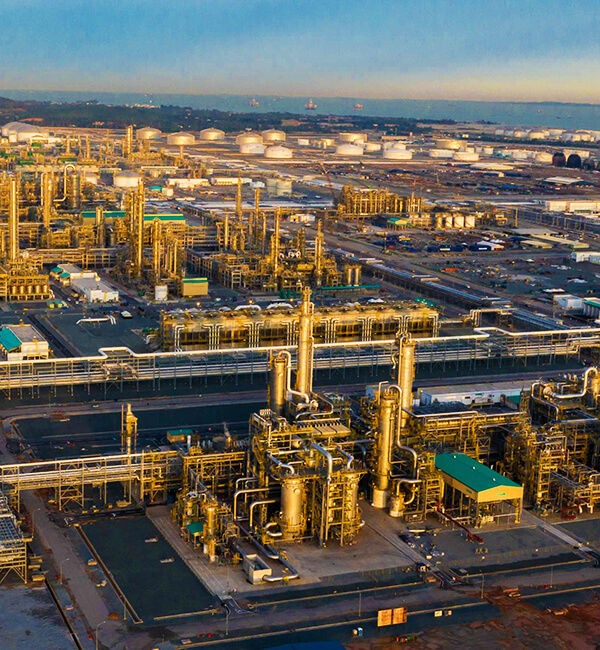
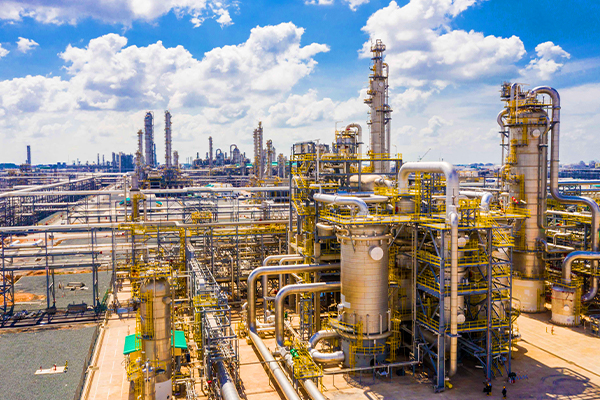
Renowned licensors such as BASF, LyondellBasell, INEOS and Shell MASTER Process - names synonymous with proven and excellent commercial reliability - provide the technologies in the Petrochemical Complex.
Cutting-edge technologies seen for the first time in Malaysia include the specialty chemical Isononanol process from BASF, as well as processes for Ethylene Oxide and Ethylene Glycol (EOEG) production by Shell MASTER Process Technology.
The Polypropylene (PP), Low Density Polyethylene (LLDPE), and High Density Polyethylene (HDPE) plants in the complex are designed to manufacture 60 different grades - 19 PP, 14 LLDPE and 27 HDPE.
Major equipment in the Petrochemical plants are mostly electrical-driven, operating at high levels of energy efficiency.
To store the polymer products, a fully automated Automatic Storage & Retrieval System (ASRS) warehouse, the first such facility in the ASEAN region, integrates packaging, storage, retrieval and logistics for distribution. It features 84,672 storage locations stacked up to 14 levels in a single warehouse building.