Why It Matters
It is our responsibility to always prioritise the health and safety of our people.
Inculcating a strong Health, Safety and Environment (HSE) culture in our organisation safeguards our employees and helps boost their morale. This enables our workforce to deliver excellence in their day-to-day activities, which in turn leads to better productivity.
Upholding good HSE practices is also crucial for our operating licence. By maintaining high standards and regulatory compliance, we can better protect our assets, mitigate financial, legal and operational risks, as well as maintain the trust of our stakeholders.
To ensure that we adhere to the best HSE practices in our industry, we are also guided by our HSE policy, which outlines our commitment and principles towards achieving our HSE vision and goals. Additionally, we have obtained various HSE certifications that demonstrate our compliance with international standards and regulations. These include ISO 14001 and OHSAS 18001.
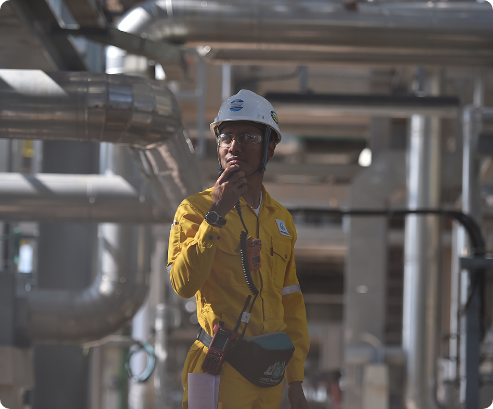
Our Approach
Through our HSE Strategy, we strive to achieve best-in-class HSE performance throughout our operations and instil a generative HSE culture within our organisation.
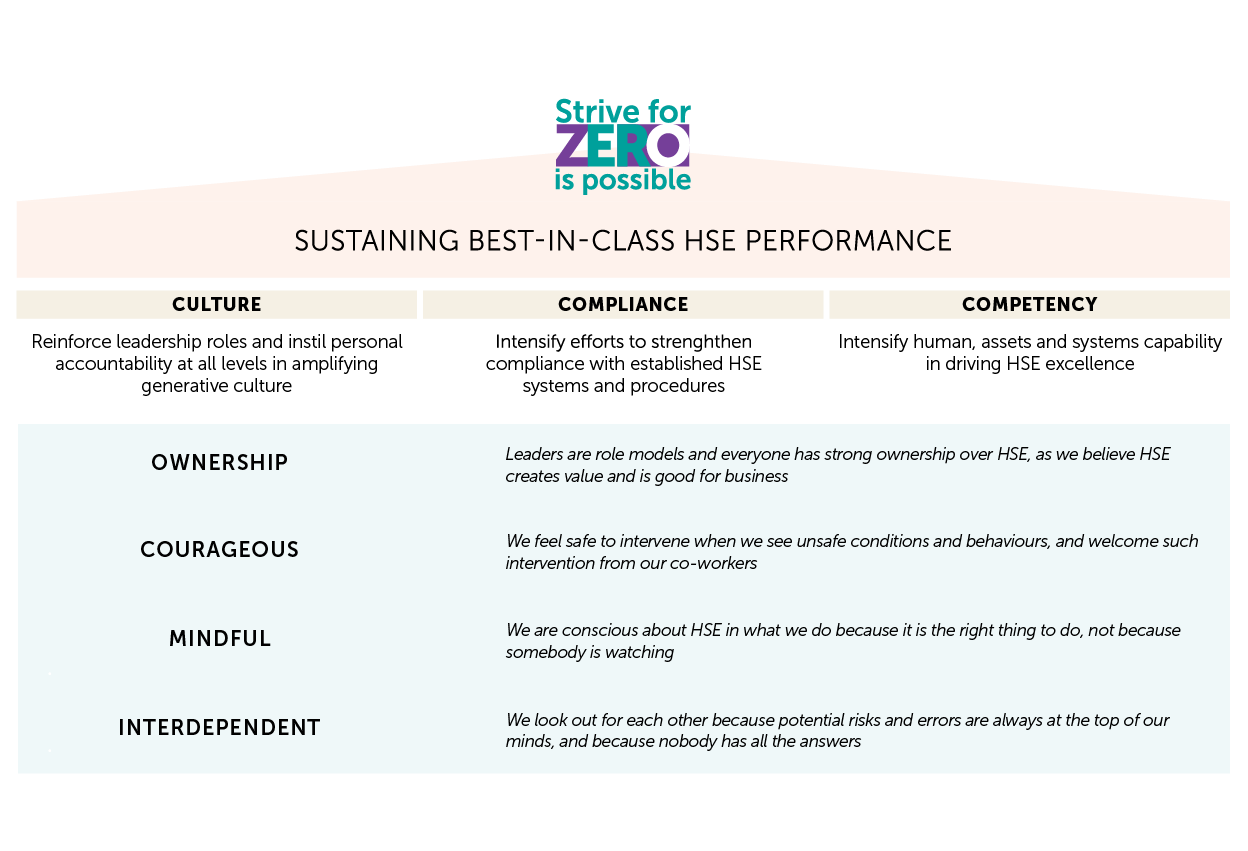
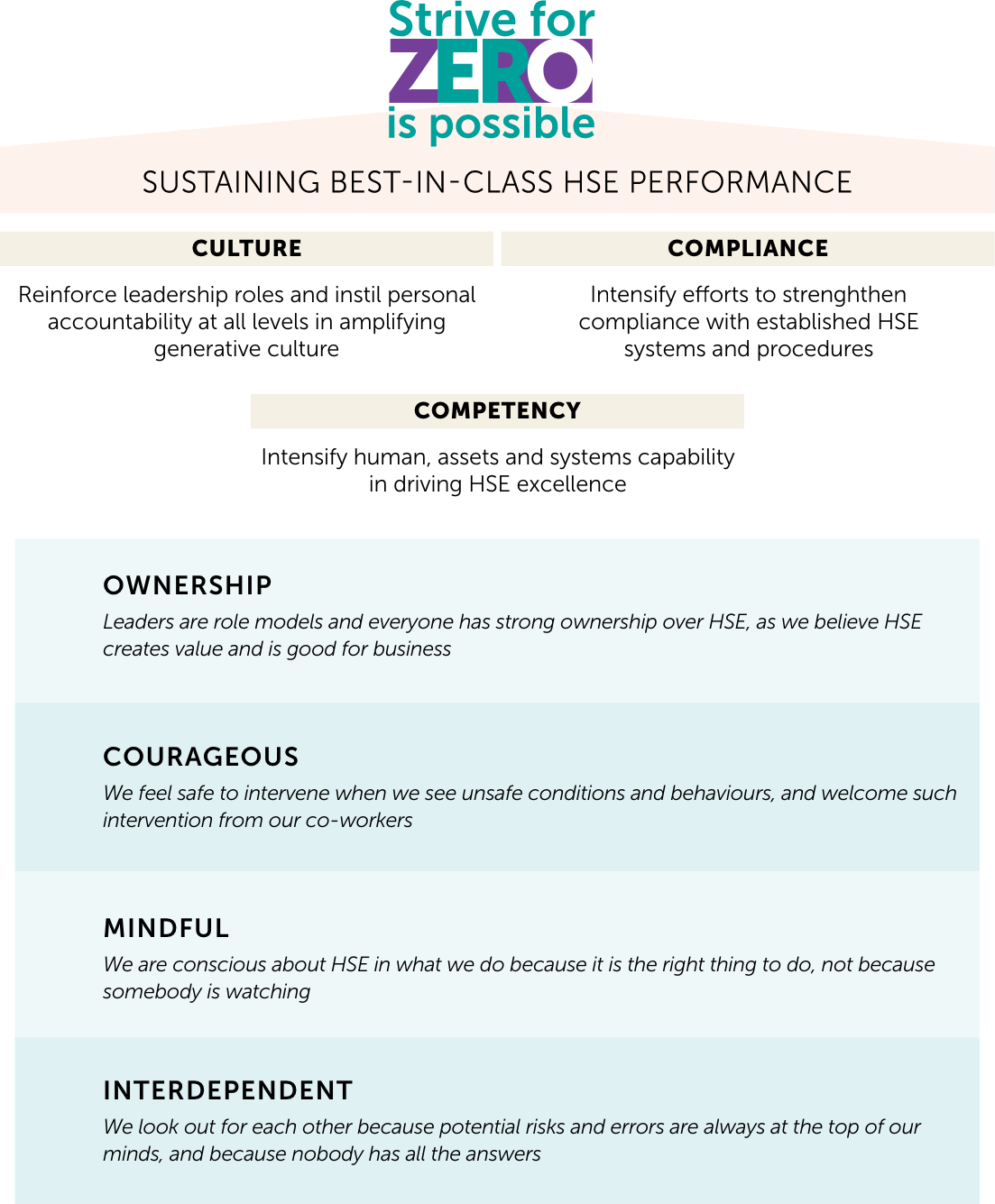
How We Provide Value
01
Culture
We continue to cultivate a robust health and safety culture by driving our Generative HSE Culture through targeted programmes aimed at achieving HSE Excellence and preventing incident recurrence. This is accomplished through:
- Enhanced FELT Leadership Engagement: Streamlining our FELT Leadership Engagement Program, led by top leaders, to ensure impactful interaction and guidance.
- Prioritised Frontline Engagement: Focusing on direct engagement with frontliners at our Operating Production Units (OPUs) to boost site leadership team motivation and foster a strong safety mindset.
- Expanded Awareness Platforms: Utilising diverse platforms such as Leaders Reach Out, FELT Leadership Engagement, Open Mic, and Share4Care to raise awareness and promote open communication.
- Contractor Integration: Instilling a Generative HSE Culture among our contractors through initiatives like the PCG HSE Partnership Pledge 2024, conducted for the second consecutive year, to reinforce shared safety responsibilities.
- Improved Process Safety Observations (PSOs): We have optimised Process Safety Observations (PSOs) by integrating them into the Unsafe Act Unsafe Condition (UAUC) platform. A new monitoring dashboard allows us to analyse quarterly PSO data, enabling continuous improvement and proactive risk mitigation.
- Reinforced Compliance with 8 Golden Rules of Process Safety (8GRPS): We have strengthened compliance with the 8 Golden Rules of Process Safety (8GRPS) by developing and distributing targeted communication materials.
- Holistic Employee Well-Being: We are committed to providing comprehensive access to non-occupational medical and healthcare services, including medical benefits, preventive health screenings, health awareness programmes, and holistic wellness support.
02
Compliance
- Standardised HSE Best Practices: We successfully deployed standardised HSE best practices during turnarounds at key facilities, and through comprehensive review workshops, we evaluated the effectiveness of these practices and identified areas for continuous improvement. To ensure the ongoing efficacy of our HSE initiatives, we have established robust tracking and monitoring systems.
- Enhanced Contractor HSE Accountability: We closely monitor contractor performance against four key performance indicators, ensuring their active participation in programs that promote a "Strive For ZERO, ZERO Is Possible" mindset, strong leadership engagement, effective grievance management, and collaborative engagement within our Contractor HSE Community of Practice (CoP).
- Digital Transformation with Digital Permit: We implemented a digital permit system across our Operating Units (OPUs), significantly enhancing operational safety and efficiency. The system improved process compliance, reduced permit processing time, and enhanced document management. The digital system's application was expanded to cover both process and non-process areas across multiple operational units.
- Strengthened Regulatory Compliance: We have reinforced our First Line Assurance (FLA) implementation by upskilling our HSE personnel and promoting the use of the Operational Legal Areas Functional Checklist.
03
Capability
- We strengthened HSE capability by implementing mandatory programs for employees, vendors, and drivers, ensuring competency through targeted training, mandatory e-learning, competency assurance, and continuous monitoring.
04
Health
- We focused on integrating health measures by collaborating with medical experts, monitoring performance through regular reports, providing health-related communications, and ensuring dedicated occupational health support.
Management Approach
Governance & Economic
Dimension
Dimension
Environmental
Dimension
Dimension
ESG Performance Data
Governance & Economic
Dimension
Dimension
Environmental
Dimension
Dimension
Together.
Harnessing Potential.
Harnessing Potential.
PETRONAS Chemicals Group Berhad Sustainability Report 2024